Extraordinary Design Solutions
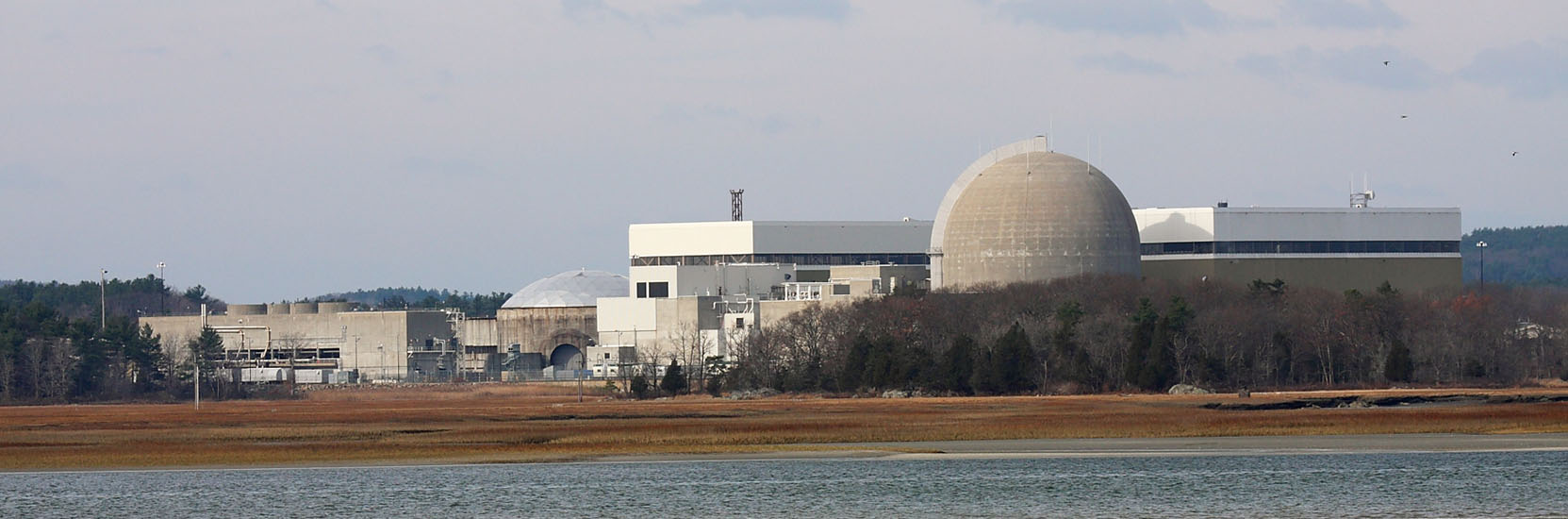
Custom Steel Hatch-EJ solves a unique problem at Seabrook Station Nuclear Power Plant
AFTER THE 2011 TŌHOKU EARTHQUAKE AND TSUNAMI, WHICH CAUSED MELTDOWNS IN THREE FUKUSHIMA REACTORS, NUCLEAR POWER PLANTS AROUND THE WORLD TOOK A CLOSER LOOK AT THEIR SYSTEMS AND THE DISASTER RISKS THEY FACED.
At Seabrook Nuclear Power Plant (Seabrook Station) in Seabrook, New Hampshire, operators realized that parts of the plant were vulnerable to F5 tornadoes, which generate winds in excess of 200 miles per hour.
This wasn't an unlikely or hypothetical concern—in 1953 an F5 struck Worcester Massachusetts, about 65 miles from Seabrook Station, which leveled large buildings and left thousands homeless.
MAJOR CHALLENGES
Seabrook Station wasn’t going to blow over, even in strong winds, but tornadoes can pick up heavy objects and hurl them through the air with enormous force (in the Worcester event, a multi-ton storage tank was blown across a road). In theory, an F5 tornado can launch a one-inch steel bar at 200 mph so that it hits a surface perpendicularly, applying enormous amounts of kinetic energy to a very small area.
Designing for this possibility revealed several potential weak points at Seabrook Station, and one was an access hatch, near the reactor, that protected an emergency power supply. A new hatch was needed, with extraordinary design characteristics:
- It had to withstand the impact of a three-foot by one-inch steel bar, at 200 mph, without puncturing or shattering. In tornado design terms this is called ‘missile loading’, and equates to 7,987 ft-lbs of kinetic energy striking an area of just 0.79 square inches.
- It had to be water-resistant.
- It had to be easily opened, by one person.
- Finally, to meet strict project timelines, the new hatch had to be delivered and installed within four weeks.
Stock hatches that met all three requirements simply aren’t available. A custom access hatch was needed in a hurry, and Seabrook called on EJ to design and install a fabricated solution.
A TALL ORDER
"It really was a tall order," says EJ Facilities Manager Tim McKernan. "We started by considering one of our airport ductile iron hatches, which can bear up to 200,000 pounds on a 9" by 9" area. That’s twice the FAA requirement, but after Seabrook looked at it, they told us it wouldn’t do."
The ductile iron hatch is more than strong enough for most purposes, but the plate it’s made of is reinforced with iron ribs—Seabrook designers realized that a steel bar striking in the thinner areas between the ribs could penetrate the hatch. What was really needed was two inches of steel across the entire hatch.
That called for an entirely new hatch design. McKernan, working with EJ Technical Sales Engineer Craig Coggins, came up with a preliminary design, refined it within a day, and got to work.
The final hatch was made from a 24" by 24" plate of two-inch thick A36 steel, treated with Safety Sure Grip, a non-slip surface. To provide water resistance, a continuous gasket was cut from a single piece of neoprene, and all bolts were applied outside the gasket.
But could one person open the new hatch? Because it was made from a single slab of two-inch thick steel, the new hatch ended up weighing 560 pounds. So, the entire weight was counterbalanced with lift springs that offset that weight precisely. In its final installed form, the hatch can be lifted with "one finger", according to McKernan, comes to rest at a 45º angle, and locks in place securely and automatically.
The custom hatch was built with a 'skirt' that matched the 15" thickness of a new, poured-in-place slab and made installation fast and easy. Additionally, EJ met the tight timeframes required; the new hatch was designed, fabricated, and installed well within the four-week deadline.
LEARN MORE
Talk to an expert at EJ to find out how the innovative solutions by EJ can work for your next project. Contact us today or schedule a Lunch and Learn.