An Innovative, Cost-Effective Approach to Glycol Collection
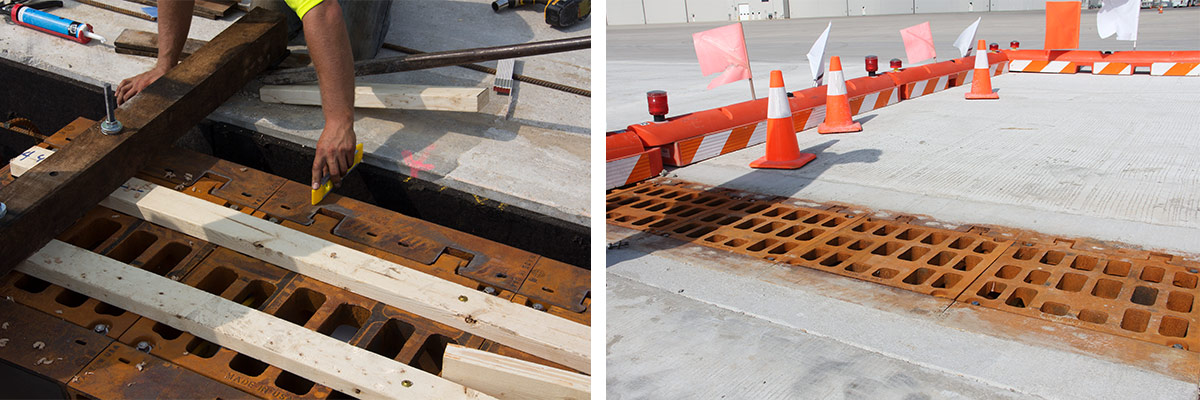
Hinged Trench Drain Installation – General Mitchell International Airport (MKE), Milwaukee, WI
Cette information est présentement disponible en anglais. Une traduction suivra sous peu.
Milwaukee's General Mitchell International Airport (MKE) is one of the largest in Wisconsin and Illinois, and is served by all major domestic airlines. MKE provides one-stop connections to more than 160 cities worldwide. In 2015, more than 6.5 million people arrived or departed through its 50 gates.
Ensuring excellent customer experiences and a safe journey for all passengers is a top priority for the busy airport. Environmental sensitivity also ranks high on MKE's list of priorities.
Recently, the Department of Natural Resources (DNR) asked the airport to increase the amount of aircraft deicing fluid (ADF) it collects. MKE needed a better solution for collecting and disposing ADF in amounts large enough to keep it in compliance. It also needed that solution to be cost-effective so it wouldn't break the budget.
RAMPING UP COLLECTION AND DISPOSAL EFFORTS
"The big hot button for the airport business right now is glycol—keeping it separate from the stormwater systems," said Lee Veldboom, P.E., technical engineering manager for EJ.
ADF is typically 95% glycol. When glycol is mixed with water, algae blooms form, which lower the amount of dissolved oxygen in the water. This endangers aquatic species living in the water source and leads to long-term water pollution issues.
"Depending on the type of aircraft, we can use 1,000 gallons of deicer on one plane," said Milwaukee County Project Manager Timothy Kipp. "It all adds up."
MKE has been recovering and disposing of glycol for years. As part of its stormwater permit with the DNR, the airport is required to capture and dispose of a certain percentage of the glycol it sprays on aircraft. Traditionally MKE used a vacuum truck system to suck the glycol off the tarmac.
Recently, the DNR has urged the airport to increase its collection amount. It was time for MKE to find a more effective way to collect and dispose of glycol, so the airport would remain in compliance.
INVESTIGATING MULTIPLE SOLUTIONS
Several collection/disposal options are available. On the high end are bio-filtration systems, which monitor oxygen levels in nearby waterways, and distilling systems, which remove glycol from the water so it can be sold to a processing plant.
A less expensive option is to slope the tarmac to a slot-drain inlet. This option creates hills and valleys on the surface of the tarmac. A bumpy surface isn't a satisfactory option for planes or passengers.
After researching solutions employed by airports in Detroit, Chicago and other northern climates, MKE decided to implement a glycol pad collection system. MKE found that virtually every large airport in locations prone to harsh winters utilize some variation of a glycol pad.
MKE opted to implement the project in phases, with Phase One being the left end of the east-west runway. In the variation MKE chose, the glycol pads are located at the ends of each runway. The glycol is collected by the capture pad and then deposited into a lift station by gravity. The lift station pumps the glycol into a 100,000-gallon tank. Once the tank is full, tankers offload the glycol and deliver it to the treatment plant.
"There are other concepts out there but this seemed to be the most cost-effective," Kipp said. "We don't generate enough to sell it back to a processing plant. We're just happy our sewage commission is happy to take it for us."
Locating the glycol pads at the end of each runway will help MKE with another government issue. New Federal Aviation Agency regulations have shortened the holdover time—the length of time an aircraft can wait after deicing prior to takeoff. Deicing as close as possible to the point of takeoff lessens the chance that the aircraft will have to be deiced a second time before takeoff. The less deicing, the better.
SELECTING THE BEST TRENCH DRAIN SYSTEM FOR THE JOB
"We knew it had to be a trench-type collection system," Kipp said.
With a trench drain, a line cut in the pavement allows the water to flow in a thin layer over the tarmac. The result: a smooth, continuous surface.
Kipp specified a hinged trench drain grate system with an extra heavy-duty load rating suitable for airport construction applications. Since MKE was using FAA Airport Improvement Project dollars, the system also had to be "Made in the USA."
In March 2015, MKE approved the 6906 Hinged Trench System by EJ for the airport construction project. Each grate section is 2-feet long with an 18-inch clear opening. The 6906 Hinged Trench System features an EON LOCK® security bolt design for enhanced security.
It met all MKE's basic requirements and then some. EJ designed the 6906 Hinged Trench System with an extra heavy-duty airport-rated top flange made of ductile iron. The flange vertically embeds into the concrete for 6-1/2-inches, locking the trench rail in place and spreading the load back into the concrete. This design reduces cracking and spalling of the surrounding tarmac.
"This trench is built for longevity," Veldboom said.
The top flange trench also features a patented self-engaging safety bar that protects workers from accidental grate closure. That gives workers an extra level of safety. The 6906 trench grate, which weighs nearly 200 pounds, can be used with hinged or non-hinged grates, but MKE specified a hinged trench for ease of maintenance.
"Our people have to get in there to clean those trenches out," Kipp said. "We decided to bite the bullet and go with a hinged product. Without a hinged trench it's just too difficult, and it could be a cause of injury in the future."
A SPEEDY, COST-EFFECTIVE INSTALLATION
The installation of the trench system for Phase One, which will allow deicing of multiple aircraft simultaneously, began the week before Labor Day of 2015.
A total amount of 2,716 linear feet of trench system needed to be placed in 300 to 500-foot sections. Veldboom and other EJ engineers were present to offer support and quality control throughout the process.
Contractor Chris Cape of Cornerstone Pavers used a non-traditional method for the installation—one that's more forgiving of site conditions. Instead of creating the trench first and then pouring the concrete apron around it, the concrete apron was poured first. Another difference: The job used expanded polystyrene (EPS) forms, custom-made to the exact shape and slope needed.
"The surface was very flat, and to get all that water to drain off was tricky," Cape said. "Putting the trench drains in post-pavement really improved the quality of the drainage. That was the main motivation for selecting this method."
Once the preparation was complete, the installation of the trench system was fast and easy. The 2-foot lengths of trench grates were bolted together to create 10-foot trench assemblies. Then the EPS forms were fastened to them. Attached 4x4s allowed the system to "hang" in position in the trench. Finally, the concrete was poured. After three days, the EPS forms were removed and the trench was complete.
"We were able to lengthen the continuous pour, so we didn't have a lot of short pours that we had to tie together," said Terry Donovan, P.E., aviation services engineer at Mead & Hunt, the construction management company for the project. "We managed to pour up to 600 -feet of trench in one day. It saved a lot of time with the curing process."
Veldboom estimates this process is 30 to 50-percent less costly compared to some installations they've seen. The trench system was complete the first week in November.
"There's not a puddle on the project," Cape said. "Everything drains perfectly."
CUSTOMER SERVICE THAT'S ABOVE AND BEYOND
"They weren't just good, they were really great..."
A successful installation wasn't the end of the involvement EJ had with the project. EJ gave the airport 52 Lift Assists for the grates as a demonstration. In February, on one of the coldest days of the year, Veldboom was back at the airport installing them.
He had to use a torch to melt the ice off the bolts, and had to periodically start the car so he could warm his hands, but he got the job done.
"It's a slick system that allows one person to open the grates," said Greg Failey, environmental manager for MKE. "We'll save some of our workers' backs, for sure!"
Everyone involved had great praise across-the-board for the responsiveness and assistance offered by Veldboom and the EJ team.
"Lee and all the guys had a lot of good recommendations that helped us give the airport a good product," said Greg Stern P.E., project manager for Mead & Hunt. "I can't say enough good things about EJ and how helpful they were."
Donovan appreciated the ongoing support EJ provided. "They were right there from the start of the project all the way through to the end," he said.
Cape notes the support EJ offered was "excellent." "They weren't just good, they were really great," he said. "Really customer-focused."
LIVING UP TO ITS PROMISE
"It's been a year now and the system's still holding up well," Stern said. "I think we've got a good product."
MKE agrees. "The project went well," Kipp said. "Last year wasn't a harsh winter and we didn't have much of a chance to see how it performed. We're looking forward to using it this year. We're expecting good results!"
LEARN MORE
Talk to an expert at EJ to find out how the innovative solutions by EJ can work for your next project.